支撐輥軸承內(nèi)圈開裂分析小結(jié)——四列圓柱軸承內(nèi)圈(2)
作者:
瀏覽:351
發(fā)表時(shí)間:2023-02-07
2、其次為四列圓柱軸承內(nèi)圈開裂的損壞分析,由軸承的受力特性及內(nèi)圈的安裝使用方式,造成內(nèi)圈開裂的外在因素主要如下:當(dāng)內(nèi)圈與軸配合過盈量偏大時(shí),軸承熱裝到軋輥輥頸后,在上機(jī)使用前,內(nèi)圈的冷卻過程中發(fā)生脹裂或在上機(jī)使用前,進(jìn)行外徑修磨時(shí)發(fā)生開裂;當(dāng)內(nèi)圈與軸配合過盈量偏小時(shí),軸承上機(jī)使用過程中,內(nèi)圈與軸發(fā)生相對滑動(dòng)摩擦,導(dǎo)致內(nèi)圈的開裂;軸承上機(jī)使用過程中,內(nèi)圈與定距環(huán)發(fā)生相對滑動(dòng)摩擦,導(dǎo)致斷面裂紋引發(fā)內(nèi)圈的開裂。軸承上機(jī)運(yùn)行過程中,內(nèi)圈與動(dòng)迷宮及定距環(huán)同時(shí)發(fā)生相對滑動(dòng)摩擦,導(dǎo)致斷面裂紋引發(fā)內(nèi)圈的開裂;分析判斷:綜合外在開裂因素及現(xiàn)象2、3分析,對輥徑進(jìn)行了測量,直接排除配合尺寸問題,故軸承內(nèi)圈端面配件與內(nèi)圈存在滑動(dòng)摩擦,導(dǎo)致內(nèi)圈端面裂紋,***終引發(fā)內(nèi)圈的軸向開裂;3、為佐證分析結(jié)果***后對損壞的內(nèi)圈進(jìn)行全面酸洗檢查,特別是內(nèi)圈的端面狀態(tài)。1、與定距環(huán)接觸的內(nèi)圈端面存在密集的摩擦裂紋;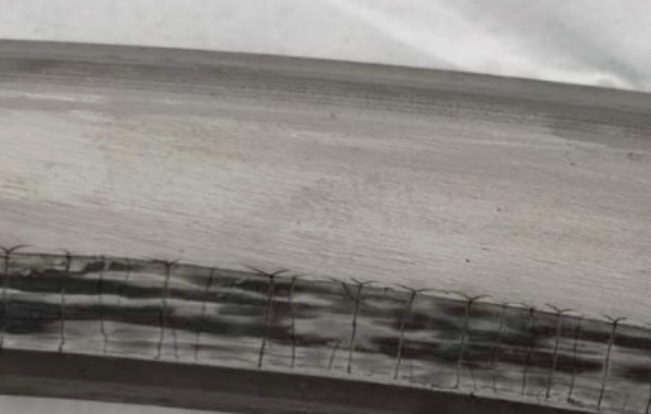
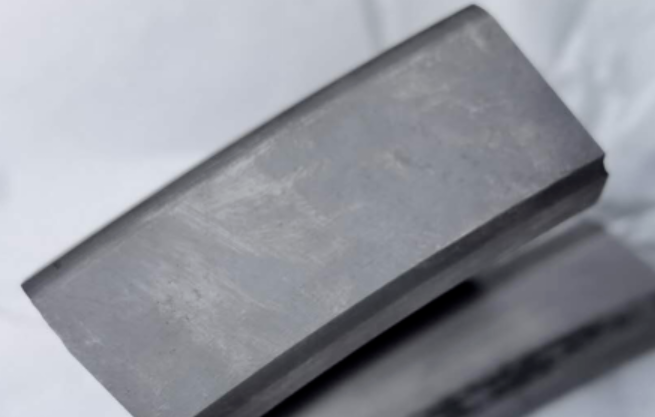
通過內(nèi)圈端面裂紋的分布查看與定距環(huán)接觸的內(nèi)圈端面存在密集裂紋,而同一個(gè)內(nèi)圈另一側(cè)無裂紋,因此可以判定,內(nèi)圈的開裂系端面裂紋引起,而端面裂紋系與定距環(huán)的摩擦引起,定距環(huán)的摩擦為定位軸承的燒損抱死引起。
本次燒故障主線為:定位軸承燒損抱死→粘鏈定距環(huán)→定距環(huán)與內(nèi)圈端面發(fā)生相對滑動(dòng)摩擦→內(nèi)圈開裂從上述分析定位軸承燒損為此次故障的導(dǎo)引點(diǎn),而內(nèi)圈端面摩擦及軸向力作用是內(nèi)圈開裂的***終原因,故預(yù)防定位軸承的抱死燒損和杜絕定距環(huán)與內(nèi)圈端面發(fā)生相對滑動(dòng)摩擦可以杜絕本次故障的發(fā)生。對使用超期時(shí)間較長的定位軸承進(jìn)行如下檢查:1、保持架是否因長時(shí)間使用兜孔磨損變大,導(dǎo)致保持架與滾動(dòng)體之間間隙變大,豎立軸承檢查滾動(dòng)體相互間距是否明顯變小或直接發(fā)生碰觸;2、內(nèi)隔圈是否磨損明顯,有無尺寸變化,導(dǎo)致軸承游隙發(fā)生改變;3、滾動(dòng)體表面是否明顯疲勞及色變嚴(yán)重,軸承需要定期進(jìn)行整體A面B面反轉(zhuǎn),杜絕單列滾動(dòng)體始終在同一個(gè)位置使用;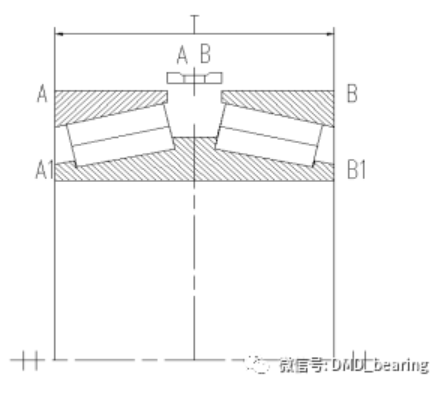
1、檢查定距環(huán)內(nèi)徑有無明顯磨損,檢查內(nèi)徑尺寸,確保與軸頸配合為過渡配合或過盈配合。2、改變與軸的連接方式,內(nèi)徑開鍵槽與軸連接或端面打孔使用螺栓與輥連接。
相關(guān)標(biāo)簽: